Study the World of Aluminum Spreading: Recognizing the Various Techniques
Light weight aluminum spreading is a basic process in the manufacturing sector, with numerous techniques utilized to create accurate and detailed elements. From the traditional sand spreading technique to the advanced die casting process, each approach offers special benefits depending on the demands of the job.
Sand Casting Method
Sand spreading, a widely-used technique in aluminum spreading procedures, entails developing molds made of compacted sand for putting molten steel. When the mold and mildew is ready, it is safely put in a flask and molten aluminum is put into the cavity.
After the metal has cooled down and strengthened, the sand mold is escaped to expose the light weight aluminum casting. Sand spreading permits the production of complex shapes and huge parts that may be pricey or challenging to generate using other approaches. It is also a lasting method as the sand can be reused and used several times, decreasing waste in the spreading procedure.
Irreversible Mold Strategy
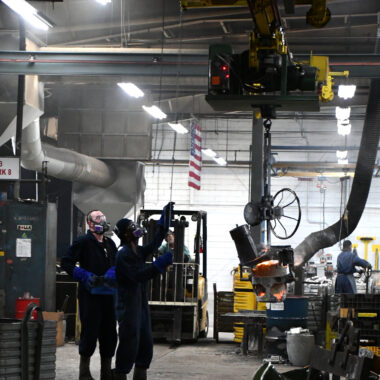
One substantial advantage of the Permanent Mold And Mildew Technique is the boosted dimensional precision it provides. The metal mold allows for tighter resistances and finer information in the last aluminum castings contrasted to sand casting approaches. This accuracy makes it a recommended selection for applications where limited dimensional control is vital, such as in the automobile and aerospace industries.
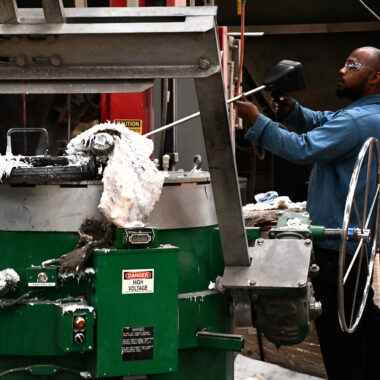
Die Casting Process

Financial Investment Casting Technique
Making use of a precision casting method, Investment Casting Strategy involves creating intricate aluminum parts by pouring liquified metal right into a ceramic mold and why not try this out mildew. This process, additionally understood as lost-wax casting, begins with the creation of a wax pattern of the desired part (aluminum casting).
Investment spreading is typically utilized for producing elements in markets where detailed styles and tight tolerances are required, such as aerospace, automobile, and clinical devices. The convenience and precision of the Financial investment Casting Strategy make it a valuable strategy in the world of aluminum casting.
Lost Foam Casting Approach
Having actually explored the complex accuracy of Financial investment Casting Approach, the emphasis currently moves to the cutting-edge approach of Lost Foam Casting in light weight aluminum component manufacturing. Lost Foam Casting, also recognized as evaporative pattern spreading, is a modern description technique where a foam pattern of the wanted component is produced and afterwards coated with a refractory material. The layered foam pattern is then hidden in sand, and molten aluminum is put right into the mold and mildew. As the steel loads the mold, the foam vaporizes due to the heat, leaving a tidy cavity in the form of the desired component.
Additionally, Lost Foam Casting is a cost-effective process as it decreases the need for cores and allows for the production of light-weight elements. In spite of its benefits, Lost Foam Casting requires careful control of the spreading process to make certain and avoid issues quality parts.
Verdict
Finally, light weight aluminum casting uses a selection of techniques such as sand casting, permanent mold and mildew strategy, die spreading, investment casting, and shed foam spreading. Each technique has its own benefits and applications, making light weight aluminum casting a flexible and widely utilized procedure in numerous industries. Comprehending the distinctions in between these approaches is crucial in choosing one of the most suitable casting method for certain see manufacturing demands.
Sand casting, a widely-used approach in aluminum casting procedures, includes creating molds made of compressed sand for pouring liquified metal. aluminum casting.The Irreversible Mold Method, like sand casting, is another prevalent method utilized in light weight aluminum casting processes, providing unique benefits in terms of mold and mildew reusability and dimensional accuracy. The metal mold permits for tighter tolerances and better details in the final light weight aluminum spreadings compared to sand spreading techniques. The 2 primary kinds of die spreading are cold chamber die casting and warm chamber pass away casting, each suitable for different kinds of aluminum alloys.In verdict, aluminum casting supplies a range of methods such as sand casting, permanent mold strategy, die spreading, financial investment casting, and lost foam spreading
Comments on “Elevate Your Assembly Line: Aluminum Casting Strategies That Provide Results”